sheet metal bending radius chart Bend Radius Chart for Mild Steel, Stainless Steel & Aluminum. When considering sheet metal design, it’s important to understand how the bend radius affects your choice of materials. In this section, we’ll discuss some . The 24V low-voltage wiring can follow the relaxed rules for low-voltage power, and be installed like thermostat wire. Here are 2 popular form-factors for 24V transformers: Mounts to a knockout on the side of a metal box.
0 · standard sheet metal bend radius
1 · sheet metal minimum bend length
2 · sheet metal inside bend radius
3 · minimum sheet metal hamtramck radius
4 · maximum thickness sheet metal bending
5 · bending steel plate minimum radius
6 · bend radius calculator sheet metal
7 · 304 stainless minimum bend radius
The National Electrical Code (NEC) includes many specific requirements for installation of outdoor circuits and equipment. With outdoor wiring, the primary safety concerns involve shielding against moisture and corrosion, preventing physical damage, and managing issues related to underground burial.
standard sheet metal bend radius
Use Xometry reference tables for sheet and aluminium to find out which bend radius is the most suitable for your sheet metal projects
Minimum Bend Radii: The minimum bend radius data shown in these charts is measured to the inside of the bend. The bend radii listed are standard minimum if manufacturing for aircraft and . Bend Radius Chart for Mild Steel, Stainless Steel & Aluminum. When considering sheet metal design, it’s important to understand how the bend radius affects your choice of materials. In this section, we’ll discuss some . Navigate your projects seamlessly with our comprehensive 90° Bend Radius Chart. Accurate, reliable, and easy to understand - a must-have tool for professionals!
junction box for range hood
sheet metal minimum bend length
Sheet Metal Bend Radius Guidelines. Here are a few key concepts to know about designing for sheet metal. Brackets, covers, cabinets, chassis, electrical enclosures. These and countless other sheet metal components might seem .
Question: My co-workers and I have been reading your columns to help us understand what tooling our shop will need to avoid overstressing our materials with small dies. We air bend our 0.125-inch-thick 5052-H32 . Instructions for Optimal Use: Input Material Thickness and Inner Radius: • Enter the precise sheet thickness and desired inner bend radius. • The calculator will instantly provide the K-factor, Y-factor, and neutral layer . One of the biggest challenges in sheet metal fabrication is ensuring the accuracy of the unfold dimensions after bending. This involves accounting for various factors such as material type, thickness, bend radius, and bend angle. . Sheet Metal Bending Calculation. Bend Allowance (BA) BA = [(0.017453 × Inside radius) + (0.0078 × Material thickness)] × Bend angle, which is always complementary. The length of the neutral axis is calculated as a bend allowance, taken at .
90-DEGREE COLD FORMING OF SHEET The radii listed are the minimum recommended for bending sheets and plates without fracturing in a standard press brake with air bend dies. Other types of bending operations may require larger radii or permit smaller radii. The minimum permissible radii will also vary with the design and condition of the tooling.
The minimum sheet metal bending height should be calculated as 2 times the thickness of the sheet metal plus the bending radius, i.e., H ≥ 2t + R. As illustrated in the accompanying figure, if the bending height is too low, the sheet metal is prone to deformation and twisting during the bending process , leading to suboptimal part shape and . Table of Contents. 1 Common Bend Radius Design Mistakes; 2 Sheet Metal Part Design for Manufacturing Tip. 2.0.1 UNABLE TO UNFOLD PART, SHEET METAL BEND RADIUS ISSUE RESOLVED; 3 How to implement the industry standard sheet metal bend radius. 3.1; 3.2 Your Partner in Precision Sheet Metal Design; 4 Sheet Metal Part Design for Manufacturing . Sheet metal bending can be done using many methods. We discuss those along with springback, bend allowances, k factor, design tips etc. . The imperial version of the bending force chart can be found here. . constant; ir – inside radius (mm); t – sheet thickness (mm) Bend allowance formulas: For bends between 0 and 90 degrees, the .
Bend Radius - As a rule, inside bend radius should be equal to material thickness. When the radius is less than recommended, this can cause material flow problems in soft material and fracturing in hard material. Bend Relief - When a bend is made close to an edge the material may tear unless bend relief is given. Figure "A" shows a torn part.Air Force Bending Chart. The Air Force Bending chart is a chart showing the tonnage used for bending different thickness sheet metal. It is useful for sheet metal designers as it specifies the bend radius and tooling to be used for different thicknesses. It is shown here for mild steel. With this chart, you can save time and increase efficiency in your bending process.. Additionally, our press brake tonnage calculator can assist you in calculating the required bending force for your specific sheet metal product.. We understand the importance of selecting the most appropriate V-opening, and our chart shows the optimum relationship between metal thickness .
junction box height
Bending is a fundamental process in sheet metal working that involves deforming a metal workpiece into a desired shape by applying force between two tools by a press brake: an upper tool (known as a punch) and a bottom tool (known as a V-die). Bending can improve a part’s structural integrity by increasing part stiffness, redistributing stress within a part, and help .
The bend’s outer edge would crack if it exceeds the minimum bend radius which is typically specified according to the metal sheet thickness (t) like 1t, 2t, 3t etc. A typical recommendation is 1t for all sheet metal parts, which means the smallest bend radius should be at least equal to the sheet thickness.
EXEMPLE 2 for metal sheet bending tables. We have a metal sheet of 5 m/m thickness in INOX (with a hardness of 70Kg/mm2), in this case we must look at the small square inserted in the table. We observe in the lower part the value T (N/mm2), the hardness of this material is 700 N/mm2, that is to say 70Kg/mm2, if we go to the C value it gives us .
where: BA is the bend allowance; B< is the bend angle; IR is the inside radius; MT is the material thickness; The K-Factor is a dimensionless value and typically ranges between 0 and 0.5 for most sheet metal materials and .You just have to insert the characteristics of the sheet metal to be bent. . Internal bending radius (Ri):: 2.5 mm. Minimum flange (B):: 13 mm. Die opening (V): 20 mm . CONFIGURE YOUR X-PRESS . CONFIGURATOR. Now that you know the tonnage and length, you can configure your press brake with our online tool and receive a customised quote. IV. Press Brake Bend Radius Calculation. The 8 times rule is a general guideline for determining the V-shaped die opening, suggesting that the V-die opening should be 8 times the material thickness. However, there is no . A sheet metal bend radius chart is a valuable tool that provides engineers and fabricators with essential information. It typically lists various materials and their corresponding recommended bend radii. Think of it as a cheat sheet for ensuring your metal sheets stay intact during the bending process. 3. The Rule of Thumb for Sheet Metal Bend .
Depth: The depth of your relief should be at least the material thickness + the bend radius + .02” (0.5mm) measured from the outside of your bend. That extra .02” provides just a little added clearance. . How to design bend reliefs for sheet metal with CAD software. There are two common ways to add bend relief to your design. One way is . So it seems I need to do the following: 1) Set up a rule that tells inventor that when using this specific sheet metal style to use the material thickness for all bend angles that are not 90degress 2) For all other bends to use the radius from the provided bend table 3) Edit the a custom unfold rule to include the kfactor, bend radius, bend .
The Sheet Metal Bend Radius Chart encapsulates essential parameters that dictate the bending process, ensuring accuracy and consistency in fabrication. Let’s explore each parameter in detail. 1. Material Type. The type of material being bent significantly influences the bending process. Different materials exhibit varying degrees of ductility . The calculated 0.375-in. radius is the minimum producible inside radius for this material and not the recommended inside radius that you see on the bend allowance chart. It’s true that the harder and thicker the plate is, the greater the minimum bend radius. The minimum inside bend radius is even larger when bending with the grain.An Air Bend Force Chart, or Force Chart breaks down a number of key components of sheet metal bending in an easy to reference format. Being able to read a bend force chart is crucial for any Brake Press operator and sheet metal engineer. The gauge, inside radius, die opening, and minimum flange length are all interconnected through different equations and relationships, the .
The bend radius is a critical parameter in sheet metal fabrication, dictating the minimum radius one can bend a metal sheet without significant deformations. Calculating the correct bend radius is essential for ensuring the structural integrity and aesthetic of the finished product. Calculating Bend Radius in Air FormingSheet metal bend calculations . CAD Hi all, . Forgot to mention that each block in the chart has 3 numbers. The large one is bend deduction and the small left one is the distance into the material to the neutral line (from the inside of the bend) , the small right one is the k factor. . Set sheet metal bend to a very small radius? Consult Bend Radius Charts: Some charts give information on the bend radius. These charts contain information relating to the numerous bend radius 610 materials, including polymer. . The sheet metal bend radius refers to the inner radius of the bent sheet metal part. This is an essential factor during sheet metal fabrication because it .

sheet metal inside bend radius
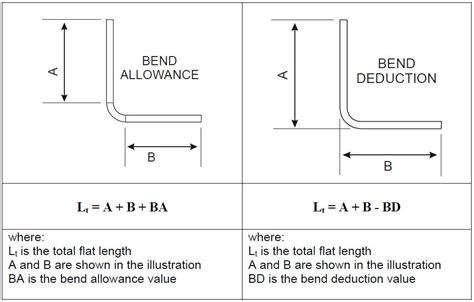
Terminal junction box wiring diagrams provide a visual representation of how the wires and connections are arranged, allowing electricians to understand the system and carry out necessary repairs or modifications. Types of Terminal Junction Box Wiring Diagrams.Understanding how to wire up outlets. Using conduit and metal boxes.
sheet metal bending radius chart|bend radius calculator sheet metal