sheet metal bending formula Mathematically k factor value is equal to the ratio of position of the neutral axis and sheet thickness. In this article, we will discuss sheetmetal bend deduction, bend allowance, K . $25.00
0 · sheet metal setback chart
1 · sheet metal flat length calculation
2 · sheet metal bending calculation formula
3 · sheet metal bending calculation excel
4 · sheet metal bending allowance chart
5 · how to calculate bending angle
6 · calculating bend allowance sheet metal
7 · bending calculation for sheet metal
View the business profile and contact info for Kevin Parks, Project Architect at Vogel Sheet Metal and Heating, Inc. in Missouri, US
sheet metal vs aluminum
sheet metal setback chart
Bend Allowance (BA) BA = [(0.017453 × Inside radius) + (0.0078 × Material thickness)] × Bend angle, which is always complementary The length of the neutral axis is calculated as a bend allowance, taken at 50 percent of the material thickness. In Machinery’s Handbook,the K-factor for mild cold-rolled steel . See moreThere are two basic ways to lay out a flat blank, and which to use will depend on the information that you are given to work with. For the first method, . See moreThere are lots of different paths to find your way around a bend, by using either the included or complementary angles. We can easily calculate these values; it is the applicationof the . See more
sheet metal flat length calculation
Learn how to accurately calculate bend allowance with our easy-to-understand formula. Improve your sheet metal bending operations and achieve precise results every time.
Mathematically k factor value is equal to the ratio of position of the neutral axis and sheet thickness. In this article, we will discuss sheetmetal bend deduction, bend allowance, K . To calculate bend allowance: Obtain the properties of the bend (bend radius, angle, and method used). Obtain the characteristics of your material (thickness and K-factor for this specific bend). Input everything into the bend .
Bend Radius - As a rule, inside bend radius should be equal to material thickness. When the . Form height to thickness ratio – To determine the minimum form height for sheet metal use the following formula: D = 2.5T + R (see below) The height can be less but it required secondaryBox Bending – The process of bending a 4 sided sheet metal box. Coining – One of the three types of bending for sheet metal where the punch penetrates into the sheet metal under high tonnage forming a consistent bend. Cross Break – .
We use the Bend Deduction formula every day at Approved Sheet Metal to compute our standard sheet metal bend gains chart. This chart serves as a handy reference for bend deductions with a variety of materials and . Use the sheet metal module or tools in the software: Most 3D CAD software provides related tools and functions for sheet metal design. For example, Creo offers a variety of methods for controlling the unfolded dimensions of sheet metal, including the modeling and unfolding methods of large arc sheet metal parts, bend deduction method, etc .BEND ALLOWANCE: Sheet metal stretches minutely as it is being formed. The greater the inside bend radius is the less the stretching. Also material hardness or elasticity has a lot to do with how much it stretches. . EMPIRICAL FORMULA: Bend allowance = (.0078 x MT + .017453 x BR) .Bend Allowance Formula. The Bend Allowance Formula takes into account the geometries of bending and the properties of your metal to determine the Bend Allowance. . Sheet Metal Bend Allowance Chart (Excel) BEND ALLOWANCE; 8 Gauge: 10 Gauge: 12 Gauge: 14 Gauge: 16 Gauge: 18 Gauge: 20 Gauge: 22 Gauge: 24 Gauge: K factor: 0.33: K factor: 0.33: K .
Sheet Metal Bending Calculator. Our comprehensive online sheet metal bending calculator is an essential tool for precision metalworking, enabling you to swiftly and accurately determine critical parameters for sheet metal bending operations. This advanced calculator provides key insights into: To understand why the K-factor cannot exceed 0.5, it’s crucial to comprehend the concepts of the K-factor and the neutral layer in sheet metal bending. Understanding Sheet Metal Bending. Sheet metal bending involves creating a controlled deformation to form a . CNC bending opens up laser cut sheet metal to a new world of possibilities, turning your 2D parts into 3D. To help make sure you get your bends the correct sizes and in the right places we’ve created a Bending Calculator tool that calculates the complicated bend allowance and bend deduction values for you. . Bend Allowance Formula and . needed as in the “standard” formula below. In fact, the “standard” formula is the radian formula plus a “built in” angle conversion from radian measure to (base 360) degrees, shown in the “Common Formula”. K R A L=? T BEND ALLOWANCE FORMULA (FOR ANGLE IN RADIANS) L= A (R+KT) A = ANGLE (RADIANS) R = BEND RADIUS
When you flatten a sheet metal part, Solid Edge uses the active settings for the Bend Equation on the Gage tab of the Solid Edge Material Table dialog box.You can use the standard formula delivered with Solid Edge, one of the example formulas delivered in the Solid Edge/Custom/Sheet Metal folder, or your own custom formulas.By default, Creo Elements/Direct Sheet Metal uses a DIN based formula as a general fall-back method for bends, hems and offsets as well as inside of the air_bend_allow function and thus implicitly in the air bending and 3 point bending processes. The name of . We are going to review three bending scenarios with three different bending angles; 60, 90 and 120, and we will calculate K-Factor, Bend Allowance and Bend Deduction for them. The bending tool has a radius of 30 mm which means that our Inside Bend Radius (R) is 30 mm. Let’s start with 90 degrees bend which is the most simple scenario.There is no perfect sheet metal bend radius formula, but within the specified bending force range, the inner radius roughly equal to the plate thickness can be calculated. Of course, the change in material thickness will affect the accuracy. Some V-shapes die openings are 6-12 times the material thickness.
Sheet Metal Bending Force Formula. In recent years, the press brake machine has gained widespread use across various industries and has expanded its processing capabilities. Despite its popularity, there has been a lack of systematic discussion on the calculation of bending .
The bending deduction in Solidworks is only used for the calculation of 90-degree bends in sheet metal. However, it can also be used for the calculation of non-90-degree sheet metal unfolding, but the bending deduction value for non-90-degree bending needs to be used according . Here you can specify many of the sheet metal specific properties including bend radius, K-factor, and bend relief dimensions. These can be fixed values or formulas based on the material thickness. (Note: you can find all of .
Hello could someone please help with a formula? I'm trying to work out the bend deduction for sheet metal parts. I have the formula but I just don't know how to input it into excel. I've attached the formula here 819554 BA ? Bend allowance θ ? Bend angle in radians or degrees r ? Inside radius; T ? Material thickness. Here is my current try =2*(M3+M5)*TAN(M2/2)-L13 6.0mm copper sheet bending allowance: 10.3; 8.0mm copper sheet bending allowance: 12.5; 10.0mm copper sheet bending allowance: 15; 12.0mm copper sheet bending allowance: 17; 3.0mm stainless steel with V25 allowance: 6; 3.0mm stainless steel with V20 allowance: 5.5; . When the electro-hydraulic servo press brake machine bends sheet metal parts, three basic parameters are required: the thickness of the sheet, the bending angle, and the position of the bending line. The first and second split . Sheet metal bending formula. Thread starter Let'sgoflying! Start date Dec 7, 2018; Let'sgoflying! Touchdown! Greaser! Joined Feb 23, 2005 . before bending. I had a bend allowance chart developed for common bend angles for each gage of sheet metal. There might be 3 or four bends across a panel but the subtracted bend allowance was very .
Since the K-Factor is based on the property of the metal and its thickness there is no simple way to calculate it ahead of the first bend. Typically the K-Factor is going to be between 0 and .5. In order to find the K-Factor you will need to bend a sample piece and deduce the Bend Allowance.How to calculate the value of material shrinkage. With this free online tool we quickly get the sheet metal bend deduction, and therefore the sheet metal blank initial flat length, from the finished part measurements. You only have to insert interior angle, flange lengths, K factor, inside radius, and material thickness.
sheet metal bending calculation formula
The following illustration shows the equation / calculation for determining the bend allowance when forming sheet metal. Most sheet metal materials will conform to the calculations. Membership Services. . Friction Formulas Apps Lubrication Data Apps Machine Design Apps Manufacturing Processes Materials and Specifications Mechanical Tolerances .
sheet metal bending calculation excel
The relationship between the bending radius of sheet metal and the width of the lower die groove of the bending die has been established through numerous experiments in sheet metal processing.. For example, when a 1.0mm plate is bent with an 8mm groove width, the ideal bending radius is R1.Y factor and K factor represent part constants used in formulas to calculate the developed length of flat sheet metal required to make a bend of a specific radius and angle in a design. Y factor and K factor are defined by the location of the sheet metal material's neutral bend line with respect to the thickness. The neutral bend line’s .
sheet metal unfold software
sheet metal vibration damping
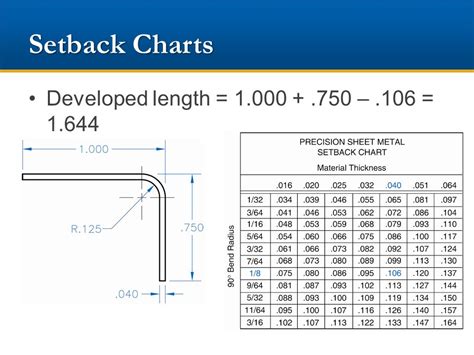
$1,800.00
sheet metal bending formula|calculating bend allowance sheet metal