sheet metal forming processes manufacturers FluidForming Americas is a quality-driven sheet metal forming company that offers manufacturers a cost-effective way to quickly — and with unbeatable . Window Flashing provides an inexpensive and easy to install method of stopping water penetration behind siding. Horizontal shelf is sloped 5-7 degrees toward outside wall. See also our XtremeTrim® for our best window flashing products.
0 · sheet metal working process pdf
1 · sheet metal stamping process pdf
2 · sheet metal processes pdf
3 · sheet metal operations with diagrams
4 · sheet metal forming process pdf
5 · sheet metal bending process pdf
6 · forming sheet metal by hand
7 · bulk deformation vs sheet metal forming
Available in over 100 luminous colours and used by artists such as Turner and Sargent, our Professional Watercolour is formulated using only the purest pigments to ensure performance and permanence.
sheet metal working process pdf
Sheet metal forming is a process used in many industries to make metal parts from thin metal sheets. It’s actually one of Xometry's most popular manufacturing methods. Our customers use the Xometry Instant Quoting .FluidForming Americas is a quality-driven sheet metal forming company that offers manufacturers a cost-effective way to quickly — and with unbeatable .The manufacturing & design guide. Learn how to effectively design sheet metal parts. This guide starts with the basics and moves toward design best practices and advice on material . How Sheet Metal Forming Optimizes Manufacturing. Sheet metal forming integrates well with modern computer-controlled manufacturing workflows for increased speed, precision, and consistency. Digital tools empower .
By understanding the various processes, materials, and equipment involved in sheet metal forming, manufacturers can optimize their operations to meet the demands of diverse industries, producing high-quality components .In this article, learn the basics of sheet metals, the various sheet metal forming processes, and how to reduce the cost of sheet metal forming with rapid tooling and 3D printed dies. For a detailed overview and the step-by-step method, .
metal bernzomatic box
In this blog, we dive into seven key sheet metal forming processes that shape modern manufacturing: Laser Cutting, Water Jet Cutting, Stamping, Welding, Roll Forming, Spinning, and Rolling.We provide fluid-cell solutions for sheet metal forming and pressing, used by major manufacturers worldwide. Global Leader in High Pressure Technology.Our top-notch machinery and skilled workers enable us to produce sheet metal parts and sheet metal components that meet and surpass your specification requirements. We form the metal to support your brand and satisfy your needs.At Prince Manufacturing, we are experts in sheet metal forming and fabrication. Metal stamping and precision metal forming. Compared to casting and forging, sheet-metal parts offer the .
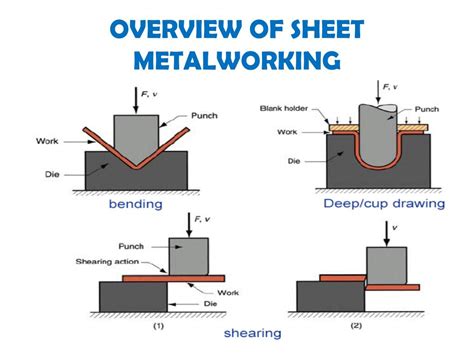
Sheet metal stamping is a cold-forming process using presses and dies to shape materials. It works with various metals, including stainless steel, carbon steel, aluminum, brass, and copper. Stamping combines cutting and forming .Metal forming processes Metal forming: Large set of manufacturing processes in which the material is deformed plastically to take the shape of the die geometry. The tools used for such deformation are called die, punch etc. depending on the type of process. Plastic deformation: Stresses beyond yield strength of the workpiece material is required.
In simple terms, The hydroforming (or fluid-forming) process is a manufacturing process that uses water pressure to shape flat sheets of metal into three-dimensional parts. This unique approach opens up a whole new world of .Sheet Metal Bending & Forming Services. Whether you need simple bends, complex geometries, or custom shapes, our experienced team is well-equipped to handle any project, big or small. . Sheet metal bending is a manufacturing process in which a flat sheet of metal is formed into a desired shape by applying force to bend it along a straight axis. Although the advantages of formability are notable, blow-forming processes, which are classified as sheet metal stretching processes, present limits in terms of uniformity of the thicknesses of the produced product.Sheet metal forming is highly prevalent in manufacturing. Sheet metal parts can be discovered in a broad spectrum of applications, such as in the automotive sector, aerospace field, consumer goods, and household appliances. . Hydroforming is a specialized sheet metal forming process that utilizes high-pressure hydraulic fluid to shape the .
Bending is another common sheet metal forming process. Manufacturers usually use brake press or similar mechanical press for metal bending. The sheet metal is placed on the die, and the punch is pressed down on the sheet metal. . Stamping is a common sheet metal forming process, which uses stamping machine and die group to punch holes in .
BENDING Bending of sheet metal is a common and vital process in manufacturing industry. Sheet metal bending is the plastic deformation of the work over an axis, creating a change in the part's geometry. Similar to other metal forming processes, bending changes the shape of the work piece, while the volume of material will remain the same.
In this manuscript, we present a comprehensive overview of true digital twin applications within the manufacturing industry, specifically delving into advancements in sheet metal forming. A true digital twin is a virtual representation of a physical process or production system, enabling bidirectional data exchange between the physical and digital domains and .Polymer AM: Application in Hydroforming. Hydroforming of sheet metals is the process of forming metal components using a liquid medium at high pressure to force a metal blank into a female die. There are multiple variations of the hydroforming process, in which some processes apply the liquid medium directly to a sheet metal component, and others, such as bladder hydroforming, .2. Deformation . Sheet metal deforming processes involve changing and processing sheet metal without cutting it. Bending is one of the most critical forming processes, and it can be done using a brake machine.A sheet metal company can use this tool to bend sheet metal into V, U, and channels up to 120 degrees.
sheet metal stamping process pdf
Explore the intricate process of sheet metal forming, its applications in various industries, and the distinction between sheet and plate metal. Learn about the manufacturing processes, the challenges with plate metal, and the final shaping of parts. . like deep drawing, there is a slight and expected change in thickness, but this may also be .The forming limit diagram is a useful reference for sheet metal manufacturers. Sheet Metal Classification . There are 3 major classes of processes of sheet metal working. Cutting: Cutting is the use of shearing forces to remove material from a work piece. Technically not a metal forming process, but of extreme industrial importance.
Consistency and Reproducibility: Metal forming processes are highly controllable, which ensures consistent quality and repeatability in mass production settings. Disadvantages of Metal Forming. High Initial Costs: The tooling and setup required for many metal forming processes, such as stamping and extrusion, can be costly. These initial .Sheet Metal Forming 2.810 D. Cooper . describe different forming processes, when they might . Small flexforming tool made by additive manufacturing . Stretch forming – very cheap tooling, net thinning, slow, low formability, sheet metal up to 15mx9m Loading Pre-stretchingPrinciples of Incremental Sheet Forming Incremental Sheet Forming is a versatile manufacturing process that involves the gradual deformation of a metal sheet using a localized tool. Unlike traditional forming processes that utilize dies and molds, ISF employs a CNC-controlled tool that moves incrementally, shaping the metal sheet layer by layer. In sheet metal forming processes there is still a lack of knowledge in this field mainly due to the need of a proper modelling of sustainability issues and factors to be taken into account. . Calculation of carbon emissions in metal forming manufacturing processes with eco-bening lubrication. Trans. Namri/Sme, 38 (2010), pp. 751-758. View in .
Principles of Incremental Sheet Forming Incremental Sheet Forming is a versatile manufacturing process that involves the gradual deformation of a metal sheet using a localized tool. Unlike traditional forming processes that utilize dies and molds, ISF employs a CNC-controlled tool that moves incrementally, shaping the metal sheet layer by layer. Stamping is a manufacturing process that involves pressing or forming sheet metal or other materials using a die and a press. This technique is used to create a wide range of components, from small intricate parts to large panels, in industries like automotive, electronics, and appliance manufacturing, due to its efficiency and precision.
Processes – CNC Punching & Forming [email protected] 2024-06-17T20:57:48+08:00. Metal Punching & Stamping Services. . Sheet metal punching is a manufacturing process that involves using a punch and die set to create holes, shapes, or patterns in sheet metal. It is commonly used in various industries for fabrication and assembly purposes.
Research and development in sheet metal shaping requires knowledge within several disciplines, including materials, tribology and processing, as well as knowledge of the equipment for testing and verification. Swerim has depth knowledge in the field and good access to lab equipment. Process, methods and materials for sheet metal forming Sheet metal forming, a versatile manufacturing process that transforms flat metal sheets into complex and intricate shapes, is a crucial aspect of modern engineering. This article, written by experts in the field of sheet metal forming, provides an in-depth overview of the process, its types of processes, materials used, and the tools and .
The forming of complex sheet metal parts is expensive and requires energy-intensive inputs. The sheet parts are typically made from steel or aluminum, and production of these two metals accounts for over 10% of global anthropogenic carbon dioxide emissions (Allwood et al., 2012).Work by Cullen et al. (2012) and Cullen and Allwood (2013) suggests .FluidForming is a cost-effective sheet metal forming process designed for rapid prototyping & low- to medium-volume production. 800-497-3545. . FluidForming Americas is a quality-driven sheet metal forming company that offers manufacturers a cost-effective way to quickly — and with unbeatable levels of accuracy and repeatability — produce .The common materials used in manufacturing sheet metal are aluminum and stainless steel. The most known grades available in stainless steel are 304, 316 and 410. 304 is one of the most common grades. . Sheet Metal Forming Processes. This is a commonly used manufacturing process that helps in manufacturing the parts for tons of known and .
sheet metal processes pdf
Compared to conventional sheet metal forming processes, advantages of RPF processes are low cost (tooling), dimensional accuracy, high flexibility, and short lead-time for tooling and part, as .
sheet metal operations with diagrams
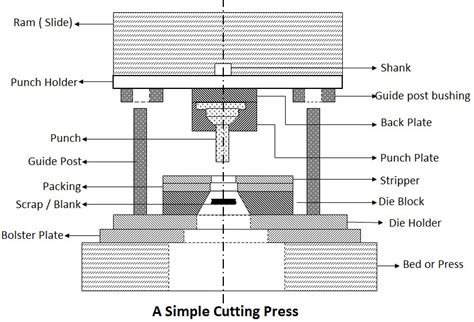
Buy Winflo 30 In. Convertible Under Cabinet Range Hood in Black with Mesh Filters and Push Button Control: Range Hoods - Amazon.com FREE DELIVERY possible on eligible purchases
sheet metal forming processes manufacturers|sheet metal forming process pdf