flange length in sheet metal Sheet Metal gauge chart converts sheet thickness from gauge to mm or inch. . BOTA BOX CABERNET SAUVIGNON SINGLE 500 ML TETRA. Jump to content Jump to search Get discounts through SMS! Sign Up (719) 635-0050 3260 Centennial Boulevard, Colorado Springs, CO 80907; facebook. instagram. tiktok. Home. About Us. Shop. Beer; By Type. Explore. Spirits; By Type. By Country. Explore. Wine; By Style. By Varietal. By Country. By .The Random House Publishing Group, a division of Penguin Random House, has entered into an agreement to acquire BOOM! Studios, the world-class comic book, graphic novel and licensed storytelling publisher and .
0 · sheet metal minimum bend length
1 · sheet metal dimensioning standards
2 · sheet metal dimensioning guidelines
3 · minimum flange length sheet metal
4 · minimum bending radius sheet metal
5 · maximum thickness sheet metal bending
6 · hole to distance sheet metal
7 · extruded hole in sheet metal
Organizers and Storage —Portable box with removable tray for extra storage, this durable all steel toolbox is ideal for storing various tools, tackle, or crafts. Equip with Handle — comfortable curved handle so that it not only be used in garages and warehouses, but also can be easily carried in trunks to long road trips.Dura-Panel™ is the perfect panel for the price conscious shopper. The affordability of this panel makes it the perfect fit for all your utility and special project needs. All steel 36' to 50' must be .
The minimum recommended sheet metal flange bend length avoid cracks in the bending area. It shall be equal to three times of sheet thickness plus bend radius. Minimum Sheet Metal Flange Bend Length = 3 x Sheet Thickness + Bend Radius
Sheet metal flat length can be calculated from a part 3D CAD model using cad .Sheet Metal gauge chart converts sheet thickness from gauge to mm or inch. .What is the minimum flange width for sheet metal? Factors like material thickness, bend radius, and application requirements typically determine minimum flange heights for sheet metal. In general, the flange height should be at least .
A +/- 1 degree tolerance on all bend angles is generally acceptable in the industry. Flange length must be at least 4 times the material thickness. Rule of thumb It is recommended to use the same radii across all bends, and flange .
Minimum flange length on sheet metal parts must be at least 4 times the material thickness. It is recommended to use the same radii across all bends, and flange length must be at least 4 times the material thickness.Minimum Flange and Minimum Hole. We’ve broken down our minimum bend radii into two values: minimum hole distance and minimum flange distance. Minimum hole distance specifies how . Learn how to calculate the minimum bending edge for sheet metal with our step-by-step guide. Get expert tips and ensure precise results in your metalworking projects. Close
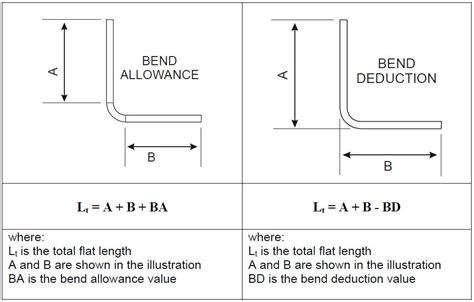
If you require flanges shorter than the minimum acceptable flange height, Approved Sheet Metal can provide a solution. They can use the "Perfect Fit Flange Formula" to design a longer flange and then cut it down using an .A zero flange would require stamping, there is no folder/bender that will give you a zero flange thickness. Have a chat to the person manufacturing. Most press brakes work on a 6 - 8 time time V size to the material thickness. i.e 3mm .
Explore 7 key techniques to enhance sheet metal parts' strength and durability, from material selection to advanced bending methods. +1(213) 398 9420 +86 13922902420; [email protected]; . Optimize Flange Length: .
Sheet metal parts are used all over and are great for enclosures and housings. 1 vin mostbet casino pin up casino lucky jet kz. HLH Prototypes, Custom Prototype Manufacturing; About. . The minimum flange length which can be applied to .An Air Bend Force Chart, or Force Chart breaks down a number of key components of sheet metal bending in an easy to reference format. Being able to read a bend force chart is crucial for any Brake Press operator and sheet metal engineer. The gauge, inside radius, die opening, and minimum flange length are all interconnected through different equations and relationships, the .Use this page to choose bend values for sheet metal that are both manufacturable and meet your needs. . Consider what minimum bend size you require (Only consider lines that meet your minimum bend requirement). . Minimum flange is the minimum distance that the edge of a flange, or particular types of cutouts (rounded slots parallel to the . I made a sheet metal drawing and i used flange for bending my part so obviously my total length changes due to the k-factor and so on. I did not use create flat pattern for my flat pattern but instead used unfold. I don't know if it matters. Now my question is can I create a parameter that indicates the total length and changes if the total length changes and how do I .
Sheet Metal Flange Issue . CAD I am trying to get the .96" dimension to be 1". I have tried all of the bending options and I keep getting irrational dimensions. . If you are using a pre-determined flat and are trying to get a specific flange length/location, then you can only adjust your bend data (inside radius/K-factor) to compensate. Reply .
sheet metal minimum bend length
There are a few guidelines you’ll need to follow to make sure that your bent sheet metal part is viable and successful. Watch the video and follow along with the guide below to help plan bends in your sheet metal parts. . Minimum Flange Length. The first thing you need to know is the minimum flange length required for your specific part .
Bends are the most typical feature of sheet metal parts and can be formed by a variety of methods and machines which negate the absolute need for some of the below tips. However for typical parts meant to be cost effective and easily produced the following tips should be useful. The minumum flange length is based on the die used to bend.If the value of sheet metal K factor and bending flange length is known. Sheet Metal flat length can be calculated in the following three steps. Step-1: Calculate the value bend allowance for the required sheet metal bend by using the below formula. Bend Allowance (BA) = (Π/180) × . It is also described as the difference between the mold line length and the flange length. Also is a crucial factor in sheet metal fabrication. In a 90-degree bend, the setback value is equal to the bend radius plus the thickness of the metal sheet. By knowing the setback size, we can determine the bending tangent position of the workpiece.
Feature-to-bend dimensions may require special fixtures or gauging. This also means that tolerances in the title block of a drawing may be unnecessarily restrictive for certain dimensions and angles, while very appropriate for others. Critical Dimensions Sheet Metal Forming – Outside dimension should be used unless the inside dimension is .
What is the minimum required Flange Length in Sheet metal Bending? The minimum flange length shall be equal to 4 times the sheet thickness plus the inside radius. Minimum Flange length = 4 X T (sheet thickness) + R (Inside Bend Radius) Flange length. You will also need to know what flange length you’ll need and if that length will work in your chosen material. (The flange is the edge of the part that’s bent from the stationary base.) . Sheet metal bending is capable of forming many difficult parts and products, but tooling does have its limitations. There are a few .Determining minimum flange length is an important step in any successful bending operation. WILA recommends a flange length that is at least 6 times the material thickness. . For more information about bending short flanges or any . The flange is the feature created on the edge of the sheet metal by bending at a defined angle, extruding at a defined length, and offsetting out or in from the selected main sheet metal feature. To create a flange on a sheet .
Pro tip: You don't always need to convert to Sheet Metal. Just draw the "L" shape (2 lines) with dimensions, go to the Sheet Metal tab and click "Base Flange/Tab". You can define the material thickness, radius, extrusion length, side material is on, etc. You can even use Sheet Metal Gauge tables to expedite the design process.You can add a sheet metal face and bend connected to an existing sheet metal face with a specified angle. . To change the side of the sheet metal face that the flange is on, click Flip Direction. Specify the following: . The corner relief type and radius size specified in the corner tab of the feature apply when you create your flat pattern .Feature placement in sheet metal design unlocks complexity and part functionality, however as sheet metal stretches during forming, features can distort if placed too close to bends. Like minimum flange length, feature proximity to a bend is dependent on material type, material thickness, and bend radius.
3. Flange Length. In sheet metal fabrication, the flange length (or flange height) is the distance between the bend and the part’s edge or the next feature, such as a hole or another bend. If a flange is too short, the sheet metal will slip into the v-shaped die during forming, preventing us from bending the material. When a sheet metal model is active (in the process of being created or edited), additional tools are available: Flange - Create a wall for each edge selected, connected to the selected edge with a bend.; Tab - Add a tab to a sheet metal flange.; Make joint - Convert the intersection of two walls into a joint feature, either a bend (walls joined by cylindrical geometry) . If possible model your part in part mode, not sheet metal mode. You can then convert the part to sheet metal, in many cases this is a more efficient way to create parts in Creo. It is much faster to create the geometry in part mode for many parts. As you have found flange is not the tool that will yield the result you want in your example model.Hi guys I am designing a sheet metal wall that has a 90 degree 2" flange bend along top. The wall needs to then taper in/bend 30 degrees at about midpoint, this bend will be perpindicular (vertically across the sheet) to the top flange bend (horizontal across sheet).
Unfolded flat size: The total length of the sheet metal when flattened; Instructions for Optimal Use: . Enter Leg Lengths A and B: • Provide the lengths of the two legs (flanges) adjacent to the bend. • The calculator will determine the total flat size of the sheet, optimizing material usage and ensuring precise part dimensions. .To add a flange feature, you select one or more edges, and specify the size and position of the material added. . Flange Property Panel Reference Defines a flange by adding a sheet metal face, a bend, and other parameters to an edge or edge loop on a face. 5.0.4 Will adjusting the bend radius to 0.030" affect the flange length of the sheet metal part? 5.0.5 Can the sheet metal fabrication team adjust the bend radius for me if my design is not optimal? Common Bend Radius Design Mistakes. Sheet metal bending can be done using many methods. We discuss those along with springback, bend allowances, k factor, design tips etc. . I can now see that the minimum flange length is 8.5 mm for such a bend, so I have to keep it in mind when designing. The required die width is 12 mm and tonnage per meter is 22. The lowest common bench .
sheet metal dimensioning standards
Whitman's started using tin for their chocolates in 1877. It isn't clear what year this tin was made, but it is an oldie! The heading of this listing mentions "Whitman's Sampler", but the word "Sampler" is not on the lid. The Whitman "Sampler" title wasn't introduced until around 1912.
flange length in sheet metal|minimum bending radius sheet metal