best tip for welding sheet metal Seam welding, or fillet welding, is one of the most common methods we use at Approved Sheet Metal. This arc welding method uses a filler rod to create a continuous weld across the entire seam of the pieces being . Custom Sheet Metal Fabrication in Wendell. Trust our comprehensive fabrication services to bring your ideas to life with expert fabrication solutions in Wendell, NC.
0 · welding tig sheet metal
1 · welding sheet metal using mig
2 · welding sheet metal
3 · welding aluminum sheet metal
4 · sheet metal welding process
5 · how to weld thin sheet metal
6 · how to weld thin metal
7 · how to weld sheet metal
To weld thin metal, choose an appropriate process (TIG or MIG with low amperage), use a smaller diameter wire or filler rod, and adjust travel speed to prevent burn-through. Employ a pulsing technique, stitch welding, or .
welding tig sheet metal
Learn why MIG, pulsed MIG, TIG and pulsed TIG are the ideal choices when welding sheet metal. When welding thin metal, the main objective is to avoid warping, burn . Sheet Metal TIG Welding Tips. 1 for 1 rule: The best way to estimate the heat input needed for welding is by applying the 1 for 1 rule. This means that 1 amp should be used per 1 . 8 Tips for Welding Sheet Metals. When wedding metal sheets, the aim is to ensure the welded parts maintain enough mechanical properties for the application. Below are tips to keep in mind as you carry out welding. 1. Select .
Choose the right type of material: MIG welding is suitable for a wide range of sheet metal thicknesses and materials, including mild steel, aluminum, and stainless steel. But you .
Seam welding, or fillet welding, is one of the most common methods we use at Approved Sheet Metal. This arc welding method uses a filler rod to create a continuous weld across the entire seam of the pieces being .
To master the art of welding sheet metal using TIG and MIG, you need to follow some tips for successful welding. You can start by choosing the right filler metal, controlling heat input, managing distortion, and ensuring . When welding metal sheet, the most important tip is to start with a clean, dust-free workspace. Cleaning off the area and placing a drop cloth beneath the work surface are essential to prevent spatter and slag from hitting . Welding thin sheet metal can be challenging because you need to obtain adequate fusion while preventing distortion and burnthrough. The key skill is to control the heat across the sheet metal to prevent defects. This guide .
It is essential to choose the right MIG electrode and wire for perfect sheet metal welding. We suggest you select the wire with the smallest diameter. Since the wire has less diameter, it also takes less heat. Hence, with less space, the .
This article will teach you how to weld thin gauge metal using each arc welding process and present the common pitfalls beginners make. While welding thin metal will test even the best welders, you can achieve great results with some know-how and practice. Learn why MIG, pulsed MIG, TIG and pulsed TIG are the ideal choices when welding sheet metal. When welding thin metal, the main objective is to avoid warping, burn-through and excessive heat-affected zones while still ensuring the weld has enough mechanical strength for the application.
Sheet Metal TIG Welding Tips. 1 for 1 rule: The best way to estimate the heat input needed for welding is by applying the 1 for 1 rule. This means that 1 amp should be used per 1 thousandth (0.001) inch of thickness. This is especially useful for carbon steel. 8 Tips for Welding Sheet Metals. When wedding metal sheets, the aim is to ensure the welded parts maintain enough mechanical properties for the application. Below are tips to keep in mind as you carry out welding. 1. Select the Filler Metals. It is essential to use a suitable filler metal that fits the mechanical features of your fabrication. Choose the right type of material: MIG welding is suitable for a wide range of sheet metal thicknesses and materials, including mild steel, aluminum, and stainless steel. But you should be careful when welding some materials like galvanized steel, as . Seam welding, or fillet welding, is one of the most common methods we use at Approved Sheet Metal. This arc welding method uses a filler rod to create a continuous weld across the entire seam of the pieces being joined.
To master the art of welding sheet metal using TIG and MIG, you need to follow some tips for successful welding. You can start by choosing the right filler metal, controlling heat input, managing distortion, and ensuring proper weld joint fit-up, to get the best results. When welding metal sheet, the most important tip is to start with a clean, dust-free workspace. Cleaning off the area and placing a drop cloth beneath the work surface are essential to prevent spatter and slag from hitting your face, clothes, or eyes. Preparation is also key.
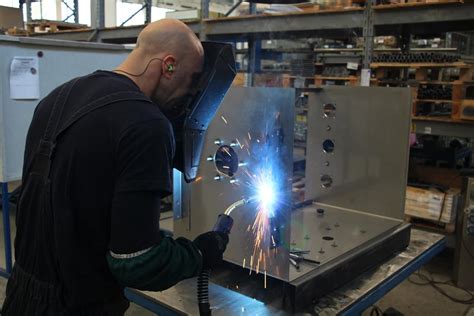
welding sheet metal using mig
Welding thin sheet metal can be challenging because you need to obtain adequate fusion while preventing distortion and burnthrough. The key skill is to control the heat across the sheet metal to prevent defects. This guide explains some of the ways to help get the best results when welding thin sheet metal.It is essential to choose the right MIG electrode and wire for perfect sheet metal welding. We suggest you select the wire with the smallest diameter. Since the wire has less diameter, it also takes less heat. Hence, with less space, the wire will burn or melt the least space on the sheet. This article will teach you how to weld thin gauge metal using each arc welding process and present the common pitfalls beginners make. While welding thin metal will test even the best welders, you can achieve great results with some know-how and practice. Learn why MIG, pulsed MIG, TIG and pulsed TIG are the ideal choices when welding sheet metal. When welding thin metal, the main objective is to avoid warping, burn-through and excessive heat-affected zones while still ensuring the weld has enough mechanical strength for the application.
Sheet Metal TIG Welding Tips. 1 for 1 rule: The best way to estimate the heat input needed for welding is by applying the 1 for 1 rule. This means that 1 amp should be used per 1 thousandth (0.001) inch of thickness. This is especially useful for carbon steel.
8 Tips for Welding Sheet Metals. When wedding metal sheets, the aim is to ensure the welded parts maintain enough mechanical properties for the application. Below are tips to keep in mind as you carry out welding. 1. Select the Filler Metals. It is essential to use a suitable filler metal that fits the mechanical features of your fabrication. Choose the right type of material: MIG welding is suitable for a wide range of sheet metal thicknesses and materials, including mild steel, aluminum, and stainless steel. But you should be careful when welding some materials like galvanized steel, as . Seam welding, or fillet welding, is one of the most common methods we use at Approved Sheet Metal. This arc welding method uses a filler rod to create a continuous weld across the entire seam of the pieces being joined. To master the art of welding sheet metal using TIG and MIG, you need to follow some tips for successful welding. You can start by choosing the right filler metal, controlling heat input, managing distortion, and ensuring proper weld joint fit-up, to get the best results.
When welding metal sheet, the most important tip is to start with a clean, dust-free workspace. Cleaning off the area and placing a drop cloth beneath the work surface are essential to prevent spatter and slag from hitting your face, clothes, or eyes. Preparation is also key. Welding thin sheet metal can be challenging because you need to obtain adequate fusion while preventing distortion and burnthrough. The key skill is to control the heat across the sheet metal to prevent defects. This guide explains some of the ways to help get the best results when welding thin sheet metal.

Welding auto body sheet metal can present challenges for welders but Ron Covell is here to help mitigate warping with both MIG and TIG welding.
best tip for welding sheet metal|how to weld thin metal