blanking process sheet metal From the basics of metal blanking to advanced techniques, this guide covers it all. Learn about the equipment used, materials processed, and applications of metal blanking. . Falls Metal Fabrication, LLC. Is a custom sheet metal shop located in Wichita Falls, TX. Our Manager/ Head Fabricator has over 40 years of experience and can help you find a way to make those difficult duct or flashing jobs easier.
0 · punching and blanking diagram
1 · perforating operation in sheet metal
2 · differentiate between blanking and punching
3 · difference between shearing and blanking
4 · difference between blanking and punching
5 · difference between blanking and piercing
6 · difference between blanking and fine
7 · blanking and piercing diagram
A low electrical humming noise can be more than just a nuisance. Learn how to find and fix a humming electrical outlet, breaker box, or appliance!
Blanking is a metalworking process involving cutting a metal workpiece into a predetermined shape, a foundational step in creating high-quality metal components. In this ultimate guide, you will discover the 6 key steps in the .The Sheet Metal Blanking Process – Step-by-Step Selection Sheet Metal Material Exam. Each project thoroughly analyzes the sheet metal types, considering strength, elasticity, and corrosion resistance characteristics. The choice of . From the basics of metal blanking to advanced techniques, this guide covers it all. Learn about the equipment used, materials processed, and applications of metal blanking. .Blanking is a crucial sheet metal fabrication process that involves cutting a flat sheet to create a flat piece or blank of specific shape and size. This process is essential in the early stages of .
In this guide, you will find all information you are looking for about sheet metal blanking. Whether you want to learn about the actual process, benefits, failure mechanism or compare it with other processes – you will find .Sheet metal blanking is a foundational fabrication technique that enables precise cutting and optimized material usage. An efficient blanking process directly contributes to product quality and cost-effectiveness. In this guide, we’ll .
Sheet metal blanking is a vital metalworking process that shapes thin metal sheets into precise tolerances for numerous applications. From material selection to finishing . What is Blanking process? Sheet Metal Blanking involves cutting a desired shape from a metal sheet. The cut-out piece serves as the final product, and the remaining sheet becomes waste. This process efficiently produces . The sheet metal blanking process involves several critical steps that must be carefully executed to ensure high-quality results. The common steps include material selection, designing the punch and die, setting up the blanking equipment, performing the blanking operation, and finishing and inspection. Let’s discuss these steps in detail. The sheet metal blanking process involves a press, punch and die system working on a metal sheet. It takes the following form: i. The metal sheet is positioned over the die containing the desired geometry cutout within the blanking press. The punch above the sheet is also in the desired part shape. ii.
Blanking is a metalworking process involving cutting a metal workpiece into a predetermined shape, a foundational step in creating high-quality metal components. In this ultimate guide, you will discover the 6 key steps in the blanking process that are essential for achieving high precision in sheet metal products.The Sheet Metal Blanking Process – Step-by-Step Selection Sheet Metal Material Exam. Each project thoroughly analyzes the sheet metal types, considering strength, elasticity, and corrosion resistance characteristics. The choice of alloys, whether malleable aluminum, robust stainless steel, or any other, depends on the requirements for the . From the basics of metal blanking to advanced techniques, this guide covers it all. Learn about the equipment used, materials processed, and applications of metal blanking. Read on for the ultimate guide.Blanking is a crucial sheet metal fabrication process that involves cutting a flat sheet to create a flat piece or blank of specific shape and size. This process is essential in the early stages of manufacturing, providing the foundation for subsequent forming, bending, or other processes.
In this guide, you will find all information you are looking for about sheet metal blanking. Whether you want to learn about the actual process, benefits, failure mechanism or compare it with other processes – you will find all information right here.
punching and blanking diagram

perforating operation in sheet metal
Sheet metal blanking is a foundational fabrication technique that enables precise cutting and optimized material usage. An efficient blanking process directly contributes to product quality and cost-effectiveness. In this guide, we’ll discover a detailed breakdown of the 9 steps involved in sheet metal blanking. Sheet metal blanking is a vital metalworking process that shapes thin metal sheets into precise tolerances for numerous applications. From material selection to finishing operations, each phase of the blanking process plays an important role in producing quality parts while minimizing waste.

What is Blanking process? Sheet Metal Blanking involves cutting a desired shape from a metal sheet. The cut-out piece serves as the final product, and the remaining sheet becomes waste. This process efficiently produces flat, uniform parts with clean edges, making it ideal for mass production of identical components.
The sheet metal blanking process involves several critical steps that must be carefully executed to ensure high-quality results. The common steps include material selection, designing the punch and die, setting up the blanking equipment, performing the blanking operation, and finishing and inspection. Let’s discuss these steps in detail. The sheet metal blanking process involves a press, punch and die system working on a metal sheet. It takes the following form: i. The metal sheet is positioned over the die containing the desired geometry cutout within the blanking press. The punch above the sheet is also in the desired part shape. ii.Blanking is a metalworking process involving cutting a metal workpiece into a predetermined shape, a foundational step in creating high-quality metal components. In this ultimate guide, you will discover the 6 key steps in the blanking process that are essential for achieving high precision in sheet metal products.
The Sheet Metal Blanking Process – Step-by-Step Selection Sheet Metal Material Exam. Each project thoroughly analyzes the sheet metal types, considering strength, elasticity, and corrosion resistance characteristics. The choice of alloys, whether malleable aluminum, robust stainless steel, or any other, depends on the requirements for the . From the basics of metal blanking to advanced techniques, this guide covers it all. Learn about the equipment used, materials processed, and applications of metal blanking. Read on for the ultimate guide.Blanking is a crucial sheet metal fabrication process that involves cutting a flat sheet to create a flat piece or blank of specific shape and size. This process is essential in the early stages of manufacturing, providing the foundation for subsequent forming, bending, or other processes.
In this guide, you will find all information you are looking for about sheet metal blanking. Whether you want to learn about the actual process, benefits, failure mechanism or compare it with other processes – you will find all information right here.Sheet metal blanking is a foundational fabrication technique that enables precise cutting and optimized material usage. An efficient blanking process directly contributes to product quality and cost-effectiveness. In this guide, we’ll discover a detailed breakdown of the 9 steps involved in sheet metal blanking. Sheet metal blanking is a vital metalworking process that shapes thin metal sheets into precise tolerances for numerous applications. From material selection to finishing operations, each phase of the blanking process plays an important role in producing quality parts while minimizing waste.
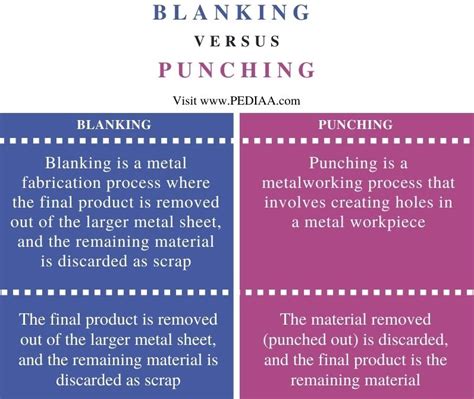
differentiate between blanking and punching

swarf removal in cnc machine
Some builders have actually used the stars as a method of signing their work, while others see them simply as decoration or a sign of "welcome." The number of points on the star can signify how formal a space is and even the color can have a specific meaning.
blanking process sheet metal|differentiate between blanking and punching