what is the minimum flange length in sheet metal bend Learn how to calculate the minimum bending edge for sheet metal with our step-by-step guide. Get expert tips and ensure precise results in your metalworking projects. In this comprehensive guide, we delve into the nuanced techniques and best practices that elevate your sheet metal welding projects to new heights. Whether you are tackling automotive repairs or creating custom metal fabrications, the finesse of stick welding can make all the difference in achieving durable and seamless results.
0 · sheet metal minimum bend length
1 · sheet metal bending radius chart
2 · sheet metal bending design guidelines
3 · sheet metal bending chart
4 · sheet metal bend deduction chart
5 · minimum sheet metal hamtramck radius
6 · maximum thickness sheet metal bending
7 · distance of hole from edge sheet metal
In this blog post, we will explore the key factors that affect MIG welding sheet metal, including wire size, gas selection, amperage, and voltage. We will also provide tips and best practices to help you achieve optimal .
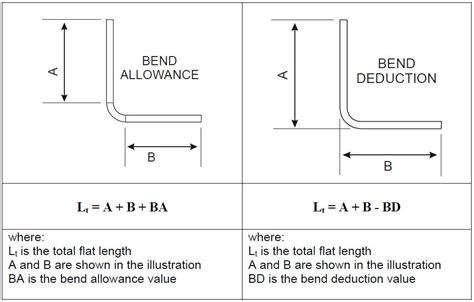
The minimum recommended sheet metal flange bend length avoid cracks in the bending area. It shall be equal to three times of sheet thickness plus bend radius. Minimum Sheet Metal . Learn how to calculate the minimum bending edge for sheet metal with our step-by-step guide. Get expert tips and ensure precise results in your metalworking projects.Minimum flange is the minimum distance that the edge of a flange, or particular types of cutouts (rounded slots parallel to the bend, rectangular or oval-shaped cutouts) can be outside of the .Minimum flange length on sheet metal parts must be at least 4 times the material thickness. It is recommended to use the same radii across all bends, and flange length must be at least 4 .
The bending force table below helps you identify the minimum flange length b (mm) and inside radii ir (mm) according to material thickness t (mm). You can also see the die width V (mm) that is needed for such .The minimum flange length is the minimum length of the straight section of material between the bend and the edge of the sheet. It's crucial to check and meet the minimum flange length .What is the minimum flange width for sheet metal? Factors like material thickness, bend radius, and application requirements typically determine minimum flange heights for sheet metal. In general, the flange height should be at least . Flange: The portion of the sheet metal that extends perpendicular to the bend axis. It is typically connected to the main body of the part. Hemming: A technique where the edge of a sheet metal part is folded over to provide a .
Generally capabilities of of 0.9mm – 20mm in thickness are able to be manufactured from sheet (<3mm) or plate (>3mm) but this tolerance depends mainly on the part. 2. Bend radii. At a minimum, the smallest bend radius . I can now see that the minimum flange length is 8.5 mm for such a bend, so I have to keep it in mind when designing. The required die width is 12 mm and tonnage per meter is 22. The lowest common bench capacity is .
sheet metal minimum bend length
Not Calculating for Sheet Metal Bend Allowance. . For example, 0.250” stainless steel has a minimum flange length of 1.150″ before the bend, while a much thinner 0.040” aluminum sheet can be bent with a flange as .The thicker or more brittle the material is the larger the radius of the bend will be. Also ask them if they use a k-factor to calculate the bend deductions or if they just have the bend deduction values for you. Radius and bend deduction numbers .In a bent sheet metal part, the flange length is the distance from where the punch bends the metal, to the edge of the part, or to the next major feature like another bend. In an air bending operation in particular, the amount of flange area left open matters a great deal.An Air Bend Force Chart, or Force Chart breaks down a number of key components of sheet metal bending in an easy to reference format. Being able to read a bend force chart is crucial for any Brake Press operator and sheet metal engineer. The gauge, inside radius, die opening, and minimum flange length are all interconnected through different equations and relationships, the .
How to determine minimum flange length. Determining minimum flange length is an important step in any successful bending operation. WILA recommends a flange length that is at least 6 times the material thickness. Furthermore, to ensure that the workpiece does not fall into the v-groove, the minimum flange length when bending on standard tools .SCS specifies that 1.2MM steel needs a bend radius of .024MM minimum. Additionally, your initial bend could be considered a "joggle" as it changes direction rapidly with little extension to the flange length. SCS specifies that for all U or C bends, the flange length must be a minimum of 2X the base length. The final bend in your first image .
For bends, the minimum distance between the inside edge of the bend and the outside of the hem should be 5 times material thickness plus bend radius plus hem radius. Holes / Slots. Distance from outside mold line to the bottom of the cutout should be equal to the minimum flange length prescribed by the air bend force chart. A: Bend radius is one parameter that determines the minimum available flange length in sheet metal bending. A bend radius will generally dictate how short or long flanges can be incorporated into a given design.Yes, but they are only theoretical and used as a guideline. Don't forget, all the values in those charts will need tweaking to suit your own tooling. The minimum detail info is how close we put the edges of holes/slots etc to the outside of the the bend. Minimum bend is the smallest outside flange length we bend in any given Vee size.
Bend deduction and flat length Calculate K factor and bend allowance for sheet metal bending Calculate length and weight of a sheet metal coil Calculate radiused bump bending Shearing force calculator Sheet metal bending parameters calculator . V-die opening and minimum flange. You just have to insert the characteristics of the sheet metal to . Table of Contents. 1 Common Bend Radius Design Mistakes; 2 Sheet Metal Part Design for Manufacturing Tip. 2.0.1 UNABLE TO UNFOLD PART, SHEET METAL BEND RADIUS ISSUE RESOLVED; 3 How to implement the industry standard sheet metal bend radius. 3.1; 3.2 Your Partner in Precision Sheet Metal Design; 4 Sheet Metal Part Design for Manufacturing . Working with an included bend angle of 60 degrees, a material thickness of 0.062 in., an inside bend radius of 0.062 in., and a bend allowance (BA) of 0.187 in., you get a negative bend deduction. That means you subtract the negative BD (again, the same as adding) when doing the flat-blank calculation.
The minimum flange length is the minimum length of the straight section of material between the bend and the edge of the sheet. It's crucial to check and meet the minimum flange length requirements specified for the material and thickness being used. Refer to the material table above for the minimum flange lengths for each material and thickness.Window bends are allowed up to 90° for sheet metal and polycarbonate parts. More acute angles require review by our team. Learn about our window bend design requirements. Joggle bends are allowed up to 90° for sheet metal parts .
sheet metal bending radius chart
3. Flange Length. In sheet metal fabrication, the flange length (or flange height) is the distance between the bend and the part’s edge or the next feature, such as a hole or another bend. If a flange is too short, the sheet .
Unfolded flat size: The total length of the sheet metal when flattened; K-factor: The location of the neutral axis relative to the inside of the bend; . Enter Leg Lengths A and B: • Provide the lengths of the two legs .
The sheet metal thickness is 0.08", bend radius is 0.05". . but for either steel or aluminium parts under 6 mm, I've kept the minimum bend radius of 1x sheet thickness as rule of thumb. . Most shops can make quite precise sheet metal parts if you follow some guidelines about radii and flange length in relation to the material and material .Typically, you shouldn't have a bend radius less than the material thickness to preverent cracking in the bend region. You may be limited to what radius you can choose based on the available dies. For air bending, the inside radius is typically right around 1/6th the V-ie opening, and your minimum outside flange length will be 1/2 the v-die .CONIC TECHNICAL GUIDE vol.13 BENDING FAQ 1 (TOOL INTERFERENCE, MINIMUM FLANGE LENGTH) TECHNICAL GUIDE. PRESS BRAKE TOOLS. vol.13 BENDING FAQ 1. . A small rising bend (1.5 times the plate thickness) can be processed quickly. . SHEARING METHOD AND WARPAGE TENDENCY BY SHEET METAL MACHINE) vol.12 TYPES OF . Flange length. You will also need to know what flange length you’ll need and if that length will work in your chosen material. (The flange is the edge of the part that’s bent from the stationary base.) For sheet metal bending with SendCutSend, the minimum flange length varies by material and thickness.
In sheet metal fabrication, curving sheets according to a specific bend radius is one of the most common operations used to create flanges, curls, seams etc.Moreover, bending imparts much strength to the sheet metal compared to their flatter counterparts. For example, an aluminium sheet bent into a V cross section will be much stiffer and stronger than the same flat .
The flange tool makes it easier to punch in the numbers for what you are trying to do, then solidworks uses your bend data to generate the flat to match. If you are using a pre-determined flat and are trying to get a specific flange length/location, then you can only adjust your bend data (inside radius/K-factor) to compensate.If the value of sheet metal K factor and bending flange length is known. Sheet Metal flat length can be calculated in the following three steps. Step-1: Calculate the value bend allowance for the required sheet metal bend by using the below formula. Bend Allowance (BA) = (Π/180) × . Required bending force to bend metal sheet of 1 meter length; V-opening width; Minimum flange length. How to Select the Most Appropriate V-Opening? The V-opening refers to the distance across the lower die mouth, and the appropriate V-opening of the die should be selected according to the sheet metal thickness. The air bending chart above shows .
How to determine minimum flange length. Determining minimum flange length is an important step in any successful bending operation. WILA recommends a flange length that is at least 6 times the material thickness. Furthermore, to ensure that the workpiece does not fall into the v-groove, the minimum flange length when bending on standard tools .

sheet metal bending design guidelines
sheet metal bending chart
West Coast Fab Inc. is an ISO 9001:2015 Compliant producer of high quality sheet metal components and fabricated assemblies. Our sole purpose is to provide our customers with the finest precision sheet metal fabrication possible.
what is the minimum flange length in sheet metal bend|sheet metal bending chart